Our choice in favour of hydrogen marks the biggest change in the history of our company. We will drastically reduce our CO2 emissions. For this, we will be using Direct Reduced Iron technology, or DRI. This proven technology has been used since the 1960s, particularly in countries where natural gas is cheap. Our plant, however, will run on green hydrogen. This is the first time anywhere in the world that this is done at this scale. And that presents the biggest challenge for us. If not enough hydrogen is available, we can always switch to natural gas.
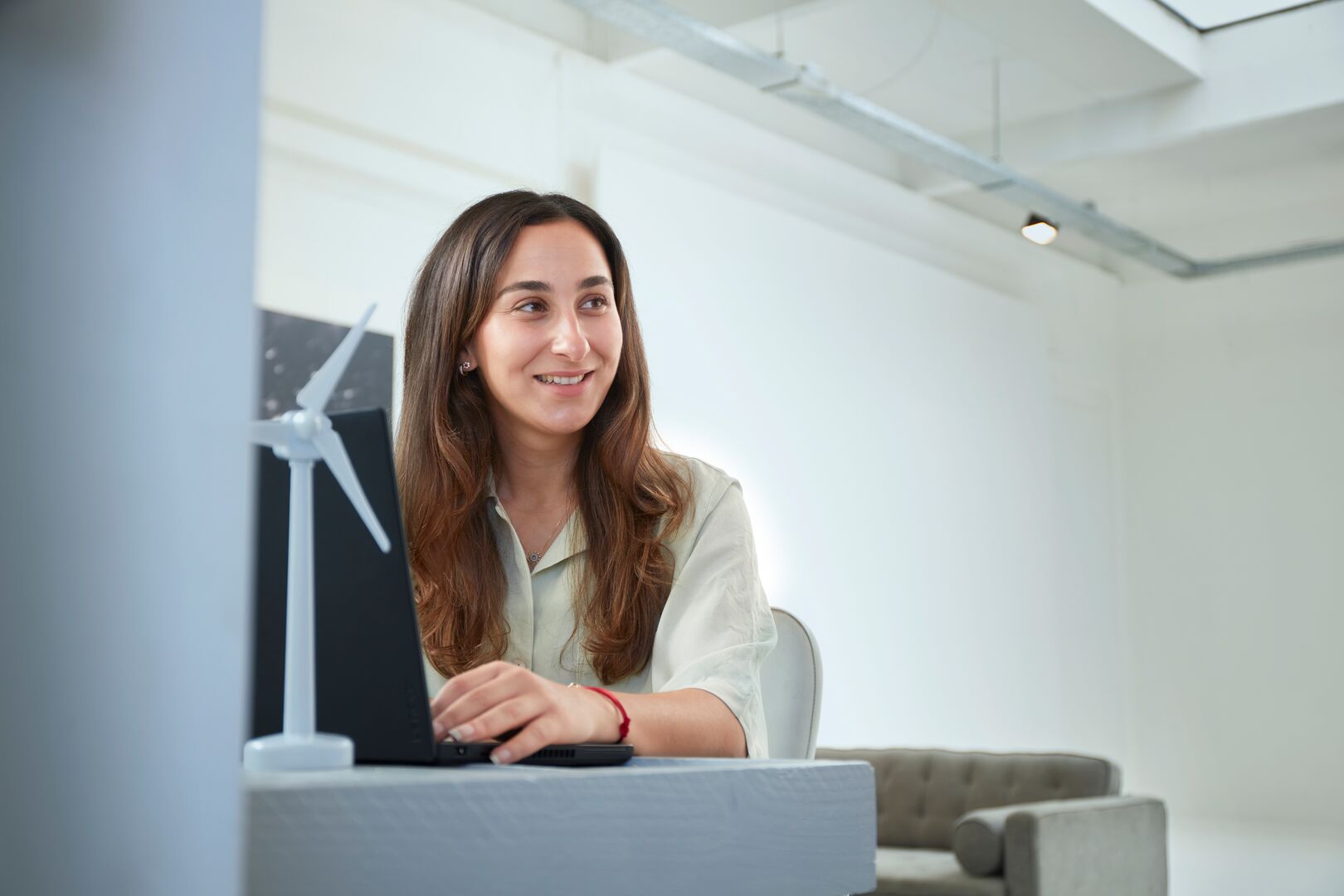
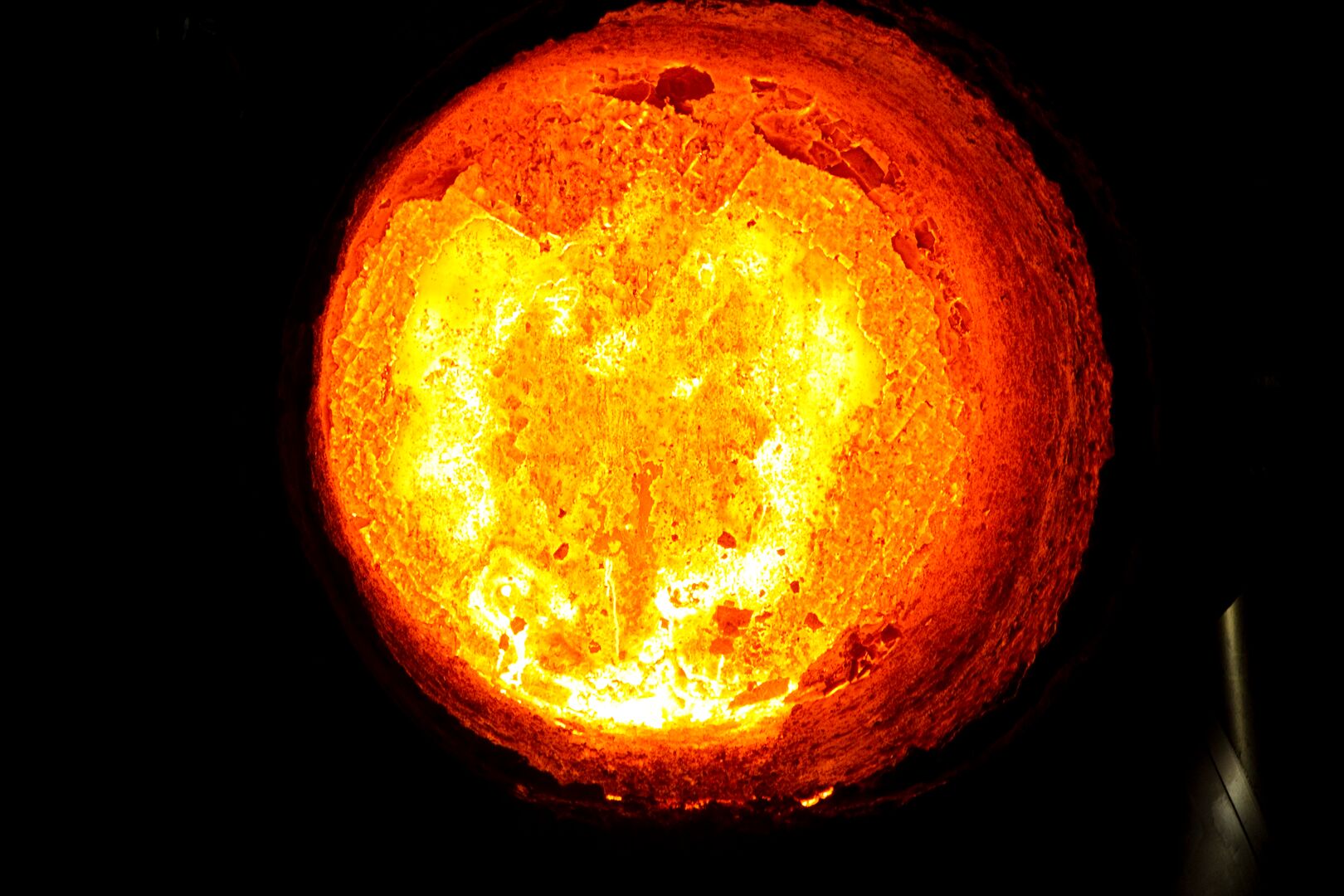
DRI technology is used to make iron in electric blast furnaces. To produce high-grade steel, the oxygen must be removed from the iron ore. This is also called reduction. Currently, we do this using coal in our Blast Furnaces. CO2 emissions are a side effect of burning coal. The new DRI technology uses hydrogen instead. This only releases water.
Reduction takes place in a shaft furnace at relatively low temperatures (approx. 1,000°C). After the oxygen has been separated from the iron ore (reduction), it is processed into hot metal in an electric furnace. The hot metal is transported to the BOS Plant by torpedoes over a new railway line. Residual gases area treated in a gas firing installation and CO2 removal plant. This way, we can reuse them in the production process.
- CO2-emissions
The use of green electricity and hydrogen considerably reduces the CO2 emissions from the primary steel process compared to the blast furnace process. - Hydrogen
Replacing coal by green hydrogen also brings about an improvement of the direct living environment. Scrap
Using scrap allows us to make steel in a more circular manner.