Steel is made from iron ore, which can be found in the earth's crust at many locations. In some places in Australia, South America, India and Scandinavia, ore is close to the surface, making it easy to extract. From all over the world, raw materials are shipped to their destination, where they are unloaded and stored using large cranes.
In IJmuiden, we produce iron from ore and coal. In 2030, we will switch to a production method that is better for the environment and the people living here: ore and hydrogen. That requires us to renovate some of the plants on our site. Until we have done that, we will continue using our Blast Furnaces.
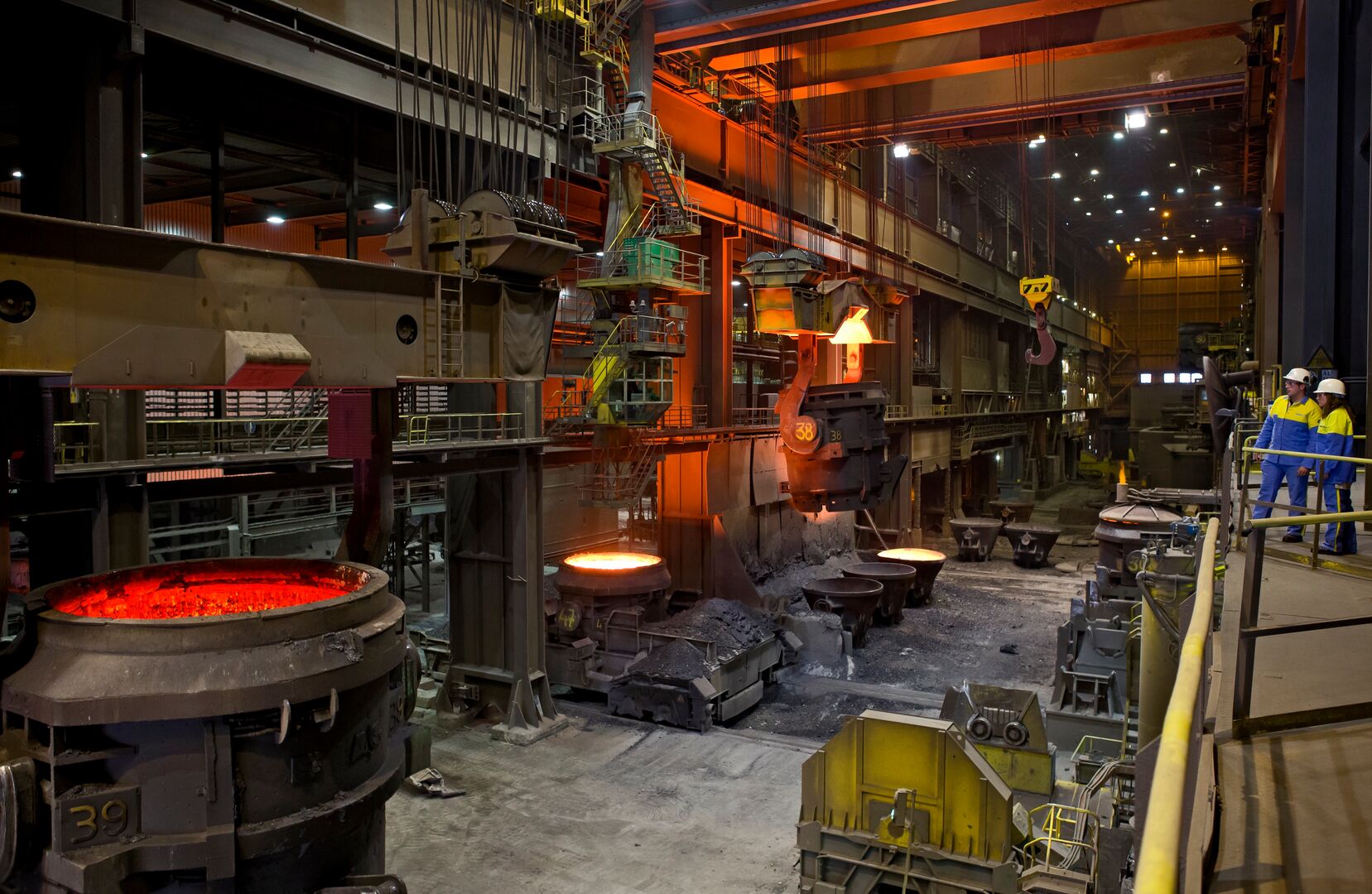
In the Blast Furnaces, we melt iron ore into liquid iron at high temperatures. Iron ore has a sand-like structure that can put out the fire in the furnace. Because of that, you can't put it in the furnace just like that. The ore is first baked to make it into porous chunks, or sinters. This is done in the Sintering Plant. In the Pelletising Plant, we turn the fine ore into small balls in large drums. These balls are called pellets.
A lift takes the sinters and pellets from the raw material bunkers to a height of 80 metres, where a dosing installation neatly layers them up in the oven.
Large amounts of hot air and finely ground pulverised coal are continuously blown into the bottom of the furnace. That heats up the furnace to 2300 degrees, the temperature at which iron ore melts. When sufficient hot metal has formed at the bottom of the furnace, we drill open the furnace and tap the iron. The hot metal is collected in torpedo-shaped train waggons and is then ready for transport to the BOS (Basic Oxygen Steelmaking) plant next door.
The converter in the BOS Plant turns the pig iron into steel. Here, we add oxygen and used steel, or steel scrap. Scrap ensures that the temperature in the converter does not rise too high and it is sustainable: empty tins, old cars, refrigerators and even bridges are reused. Steel is a pre-eminently circular product: it can be endlessly reused.
The steel is cast into slabs and further rolled into thick and thin coils in the hot strip mill and cold strip mill. These coils go to manufacturers in construction, the automotive industry, white goods, industry and food packaging.
Rolling changes the structure of the material. By rolling it in the right way, we make extremely strong steel for cars, or thin and light steel for tins. After rolling, we apply a thin layer of tin, paint, zinc or plastic coating, depending on the purpose. Then we package it before it goes to the customer.
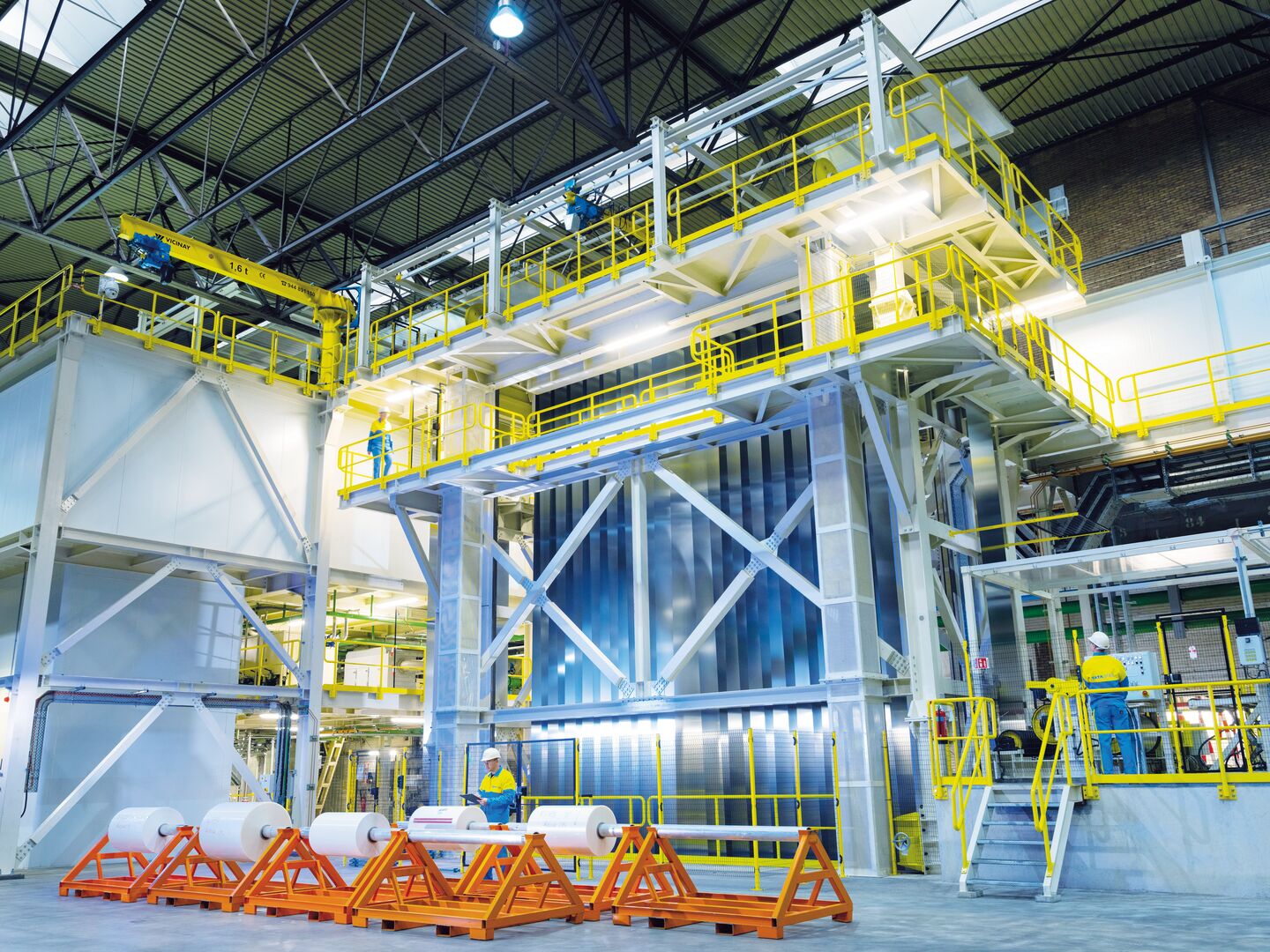