Blast Furnace 6 is currently undergoing a major repair and modernisation programme. After reparation, during which the blast furnace stood still, it is now once again ready for the future. The last time that a blast furnace was extinguished for a long period was in 1985.
It is a huge undertaking, and this will in fact be the last time that we undertake such a large-scale operation on a blast furnace. The execution of our Green Steel plans will imply that we shall in the near future say goodbye to our blast furnaces. Blast Furnace 7 is scheduled to be the first to stop operating in 2030. Blast Furnace 6 will stop operating at a later stage, which is also why it is important for it to be able to keep producing amply until then. Along with the repairs we are also building a number of measures in and around the blast furnace that should further limit the emission of harmful substances.
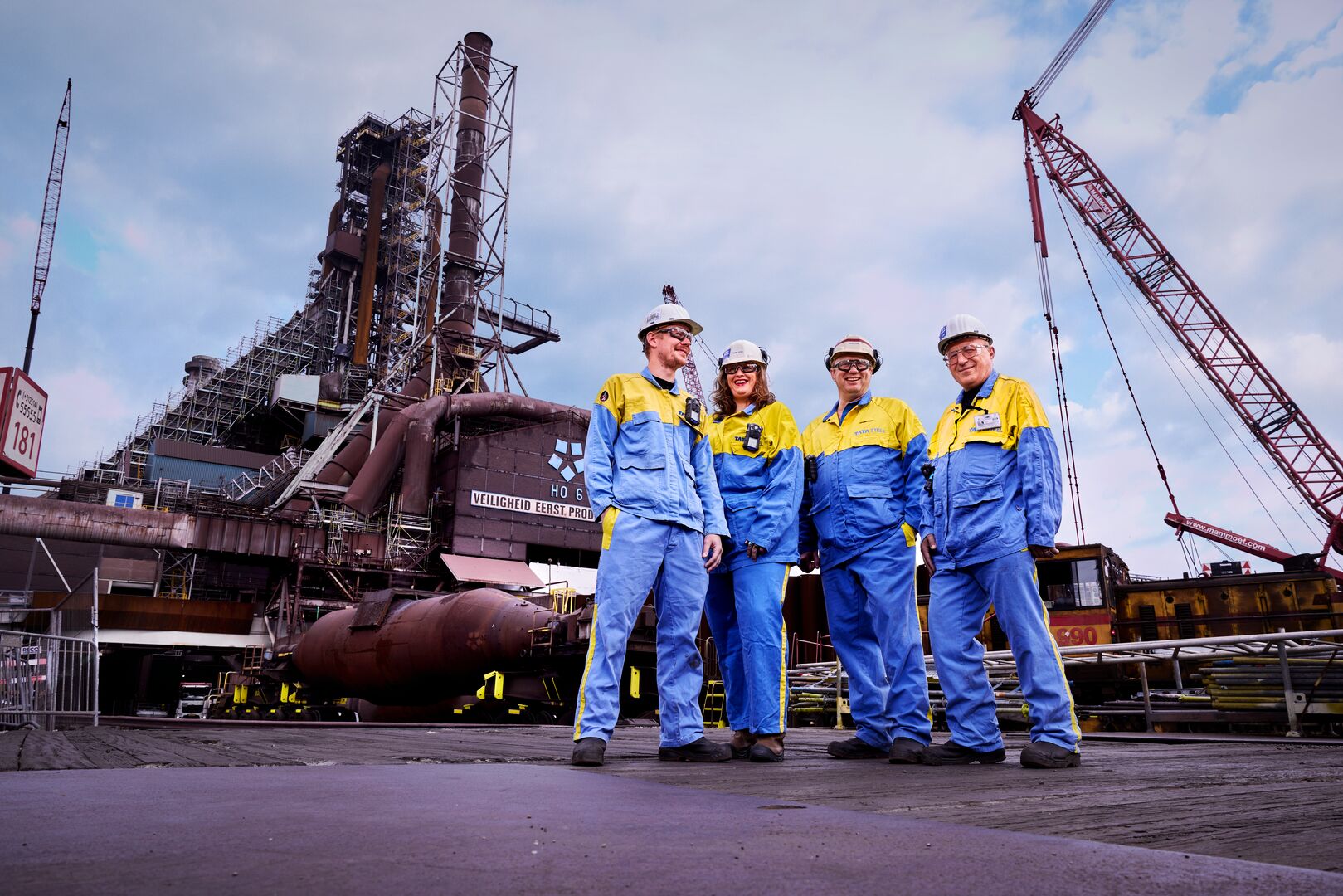
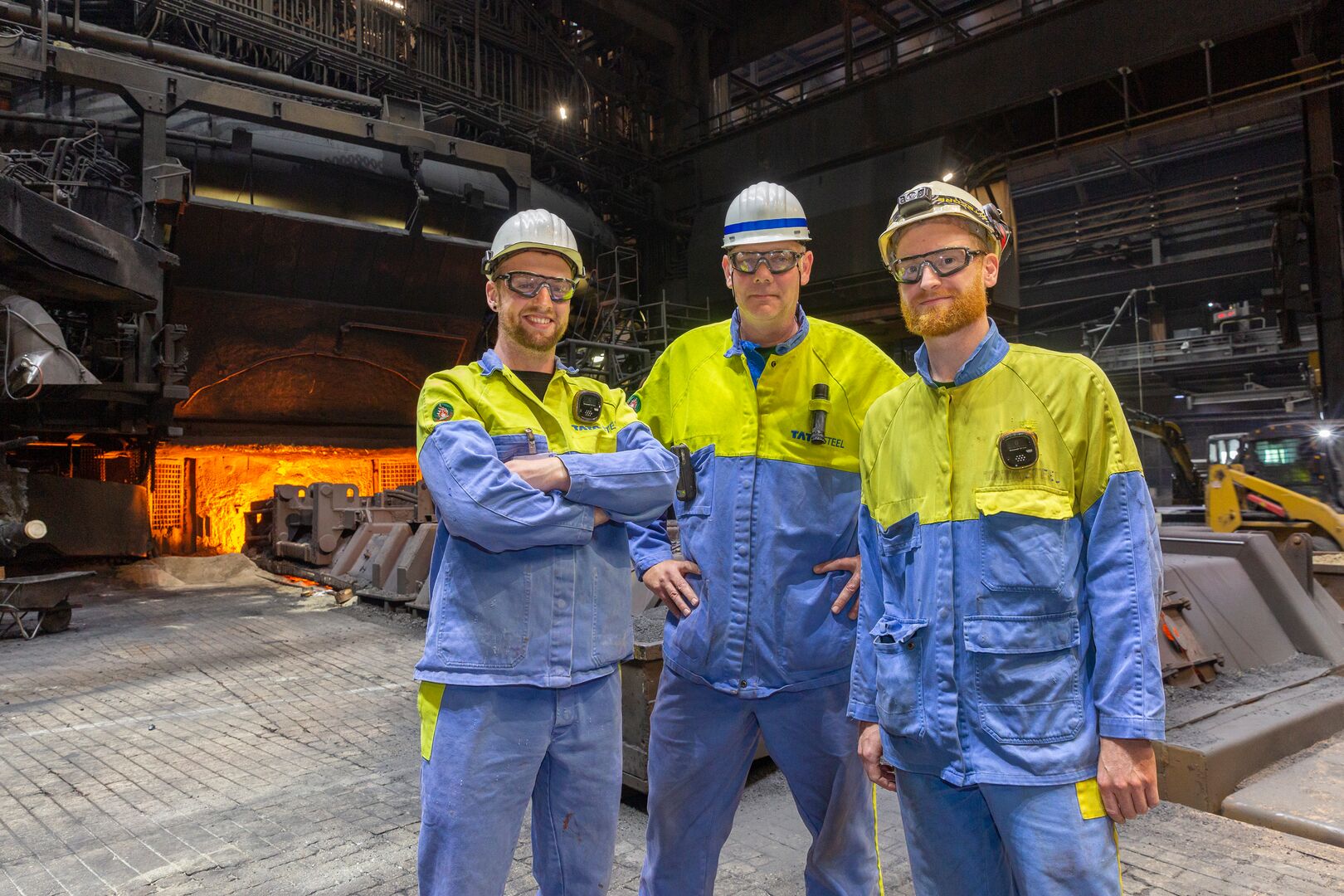
During the standstill, operating systems, all fireproof material – materials that must be able to resist temperatures of some 1,500°C – and raw material supply among others will be replaced.
Various environmental measures from the Roadmap plus programme will also be implemented, for instance the installation of three additional extractor hoods to reduce the release of dust from the blast furnace. During the opening and shutting of tap holes at the cast house of a blast furnace, dust can be released from the roof of the cast house. By placing special extractor hoods above a tap hole, the dust can be extracted in a more targeted way, thereby reducing dust emission.
The first of three additional extractor hoods have already been installed at Blast Furnace 7. The bigger extraction capacity should result in about 75% less dust emission during the tapping of hot metal.
Bigger taps, many people on the floor
Bringing a blast furnace to a standstill is a huge project that implies many considerations. A lot of time will for instance be spent on the tendering of the work, selecting the right contractors, and drawing up a plan of approach to ensure that everything is done properly and safely. Besides being a technical challenge, it also implies a huge logistic effort. Huge cranes and many people will be present on the site. During the entire period that the blast furnace will be standing still, about 1,000 extra people will be working there. Work will continue 24/7 and we shall be dealing with some 14 different nationalities.
Blast Furnace 6 was built in 1967. It is 125 metres high. The last big standstill was in 1985 (37 years ago). A small renovation also took place in 2002. Blast Furnace 6 has for years already been one of the furnaces with the lowest coke consumption in the world. Due to this – and due also to the high efficiency of the process – the CO2 emission per tonne of hot metal that the furnace produces is very low compared to other furnaces around the world. It was therefore decided to repair Blast Furnace 6 and to take Blast Furnace 7 out of production first.
What does a blast furnace actually do?
In a blast furnace, hot metal is produced by heating coal and iron ore. Special coking coal is used (not ordinary coal, but special metallurgic coal that is particularly strong, also referred to as coke). The coke comes from coking and gas plants. The iron ore must first be prepared and transformed into sinter (airy lumps) or pellets. A mixture of sinter, pellets and coke is then add layer by layer from the top in a blast furnace. At the bottom of the blast furnace the temperature is approximately 2,500°C, whereby the iron ore is transformed into hot metal. The liquid hot metal has a temperature of 1,500°C and is tapped in special torpedo-shaped railway wagons (that are fitted with fireproof material on the inside to prevent the wagons from melting). The railway wagons transport the liquid hot metal to the steel plant where large slabs of steel are made from the hot metal.
The most prominent works are indicated with numbers in the accompanying picture.
The fireproof lining in a blast furnace can resist extremely high temperatures; this is essential, considering that the temperature of the liquid hot metal is approximately 1,500 degrees Celsius. The lining in the blast furnace needs to be replaced. New fireproof brickwork will ensure the maintenance of the furnace. It will also ensure that the work environment remains safe.
Special trains (called ‘torpedoes’) take the liquid hot metal produced in the blast furnaces from the ‘tapholes’ of the furnace to the steel plant. Dust may be released when these tapholes are opened and closed.
These additional extraction facilities are expected to reduce dust emissions during the tapping of hot metal by approximately 75%.
Blast furnace gas is released during production. It is captured and cleaned by the gas cleaning system. This happens through a downcomer. Eventually the gas arrives at the stock yard and can then be reused again. These works will also be unnoticeable to the surrounding inhabitants. The repairs will contribute to reduced dust emissions.