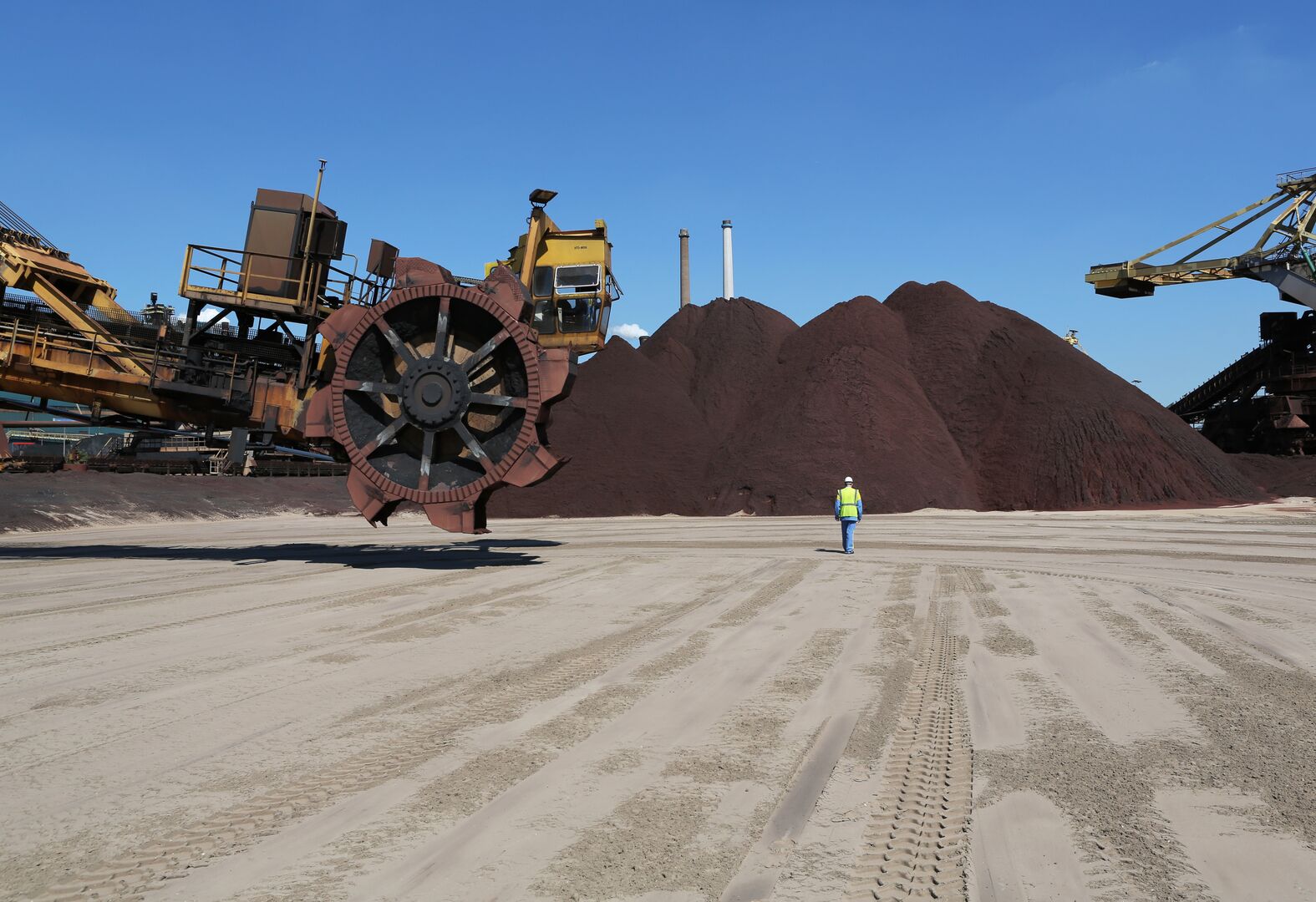
Hier worden kolen 18 uur lang verhit tot 1000 graden Celcius. Het kolenmengsel verandert in harde brokken kooks, waarbij kooksgas ontstaat dat andere fabrieken op ons terrein aandrijft. Als de kooks gaar zijn, worden deze direct geblust met water. Daarbij ontstaan indrukwekkende stoomwolken. Hierna zijn de kooks klaar voor gebruik in de Hoogovens.
Het blussen van kooks is een standaardproces dat elke 15 minuten plaatsvindt. Dit zijn de kenmerkende witte pluimen die je boven ons bedrijf ziet, vaak twee tegelijk omdat wij twee Kooksfabrieken hebben. Uit eigen onderzoek blijkt dat normaal blussen het beste resultaat geeft aangaande stofemissies.
De cijfers
- Kooksproductie: 1.8 miljoen ton per jaar
- Koosovengas geproduceerd: 115.000 m3 per uur
- Deze gassen worden 100% hergebruikt
Ertsen gaan vanaf de menghoop via de lopende band naar twee fabrieken om gebakken te worden tot sinters en pellets. De Sinterfabriek produceert brokken erts (sinter) en de Pelletfabriek maakt kleine harde knikkers (pellets).
Een moderne doekfilterinstallatie filtert de rookgassen. Hiermee wordt de uitstoot van stof en fijnstof tot een minimum beperkt.
De cijfers
- Pellets productie: 4.8 miljoen ton per jaar
- Sinter productie: 4.8 miljoen ton per jaar
- 25% van de reststoffen Sinterfabriek wordt hergebruikt
- 2025: oplevering DeNox-installatie Pelletfabriek
De twee grote Hoogovens worden van boven continu gevuld met kooks, pellets en sinter. Onderin de ovens wordt hete lucht en fijngemalen steenkool ingeblazen en ontstaat een temperatuur van ruim boven de 2.000 graden Celsius. Er komen chemische reacties tot stand waardoor vloeibaar ijzer en vloeibare slak ontstaan. Deze worden afgetapt en van elkaar gescheiden.
Het ijzer stroomt in een speciale vuurvaste treinwagon, ook wel ‘torpedo’ genoemd, die het naar de Staalfabriek brengt. De vloeibare slak wordt gekoeld met water, zodat een hoogwaardige kwaliteit slakzand ontstaat dat gebruikt wordt als grondstof voor cement.
De cijfers
- Hoogte: 120 meter
- Ruwijzerproductie: 6.5 miljoen ton per jaar
- Hoogste temperatuur: 2.300 graden Celcius
Vloeibaar ijzer gaat hier samen met staalschroot in een converter: een groot vat van zo’n 11 bij 9 meter. Door hier zuurstof bij te blazen wordt koolstof uit het ijzer verwijderd en ontstaat staal. Vervolgens maken wij het precieze staal dat de klant heeft besteld. In de gietmachine wordt het staal uitgegoten tot plakken van 15 tot 40 ton. In de Staalfabriek hergebruiken wij grote hoeveelheden staalschroot. Het nieuwe staal dat wij maken zal ooit weer als schroot terugkomen: een eeuwige kringloop.
De cijfers:
- Hoogte: 86 meter
- Staalproductie: 7 miljoen ton per jaar = 280.000 plakken staal
- 25% is afkomstig van gerecycled schroot
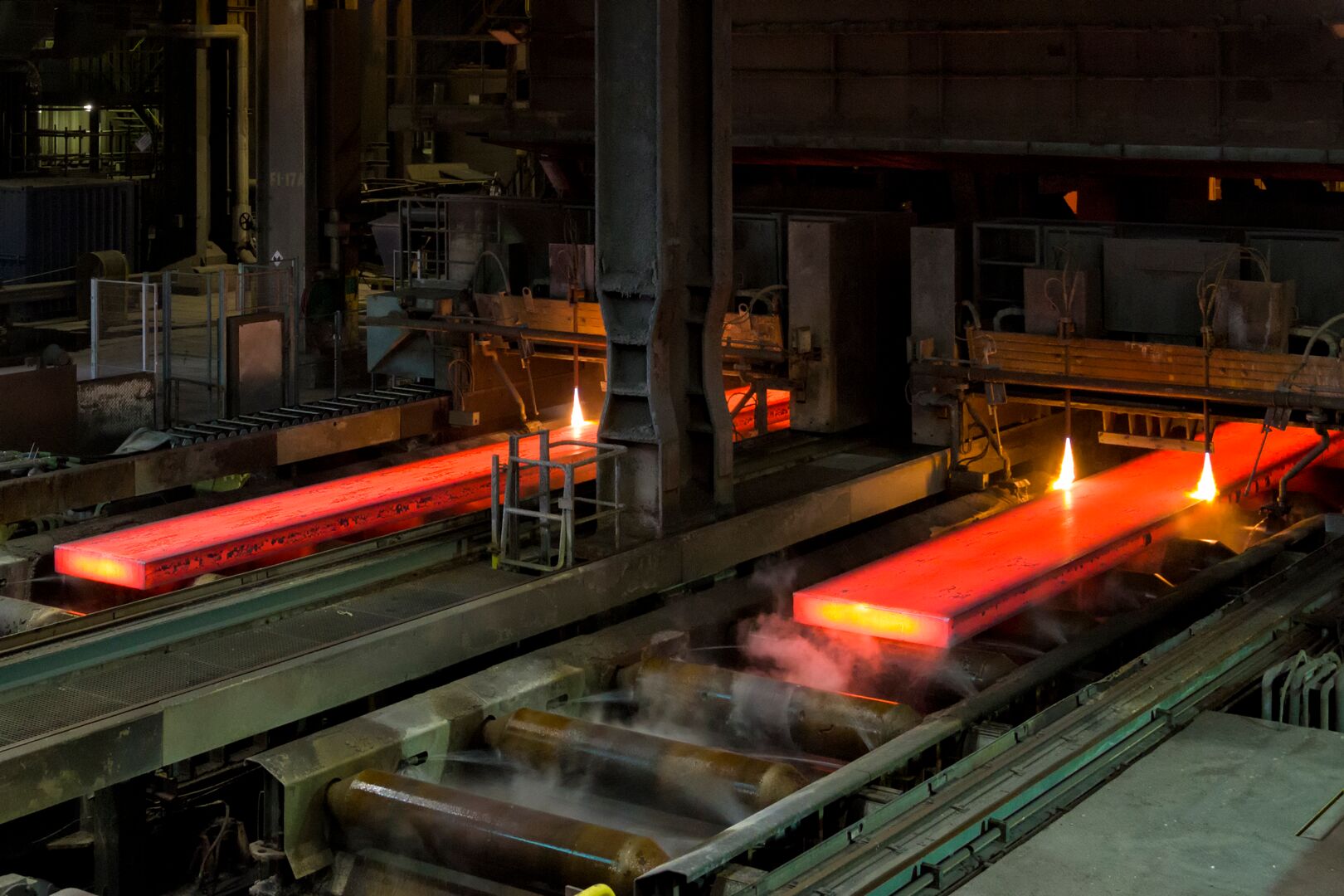
In de Direct Sheet Plant (gietwalsinstallatie) wordt het vloeibare staal in één doorlopend en efficiënt proces omgevormd tot rollen warmgewalst staal. Dit staal wordt gebruikt in elektrische componenten zoals lamellen voor elektromotoren en onderdelen van transformatoren. Maar ook in autostoelen, meubels en gevelplaten.
De cijfers
- Productie van 1.4 miljoen ton staal per jaar (70.000 rollen)
- Lengte tunneloven: 320 meter
In de Warmbandwalserij worden plakken staal verhit in een oven en vervolgens uitgewalst. Wij kunnen het staal zo dun als 2 millimeter maken. Daarna wordt het gekoeld en opgerold. Door dit proces van opwarmen, walsen en afkoelen kunnen wij nauwkeurig bepalen wat voor soort staal wij maken. Zo maken wij vervormbaar staal voor batterijhulzen maar ook heel sterk staal voor graafmachines.
De cijfers
- Productiecapaciteit: 5,3 miljoen ton per jaar = 267.000 rollen
- Maximale rolgewicht: 38 ton
- Lengte per rol: maximaal 2 kilometer (bij het dunste materiaal)
In de Beitsbaan wordt de walshuid verwijderd met verdund zoutzuur. De walshuid is een oxidelaag die ontstaan is in de Warmbandwalserij. De verwijderde oxide wordt opgevangen en later weer ingezet als grondstof. Na het beitsen krijgen de rollen een laagje olie om roest te voorkomen.
De cijfers
- Productiecapaciteit: 4 miljoen ton per jaar
Door koudwalsen wordt het staal dunner, gladder en sterker. Na het walsen gloeit het staal na onder grote stolpen, waardoor wij het makkelijker kunnen bewerken. Koudgewalste rollen staal worden voor allerlei dingen gebruikt, bijvoorbeeld in witgoed. Een deel van deze rollen gaat door naar de volgende productiestap om het materiaal te beschermen tegen roest en het daarmee duurzamer te maken.
De cijfers
- 2,4 miljoen ton per jaar
- Rolgewicht: 10-48 ton
- Dikte bandstaal: 0,3-4 mm
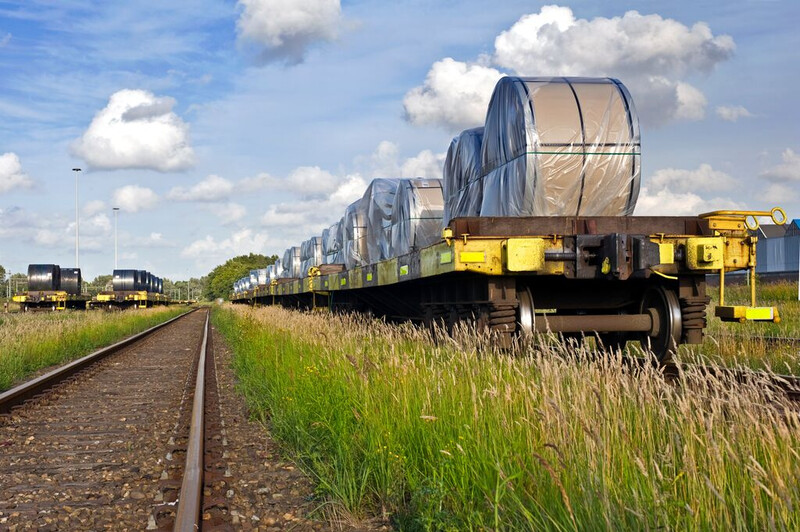
In de Dompelverzinklijnen krijgen koud- of warmgewalste gebeitste rollen een laagje zink om corrosie tegen te gaan. Dit verzinkte staal wordt toegepast in bijvoorbeeld auto’s of gevelpanelen.
Het staal doorloopt een aantal stappen en wordt vervolgens in een bad voorzien van een laagje zink met daarin magnesium en/of aluminium. Wij maken dit duurzamer met Magizinc®. Dit is één van onze speciale coatings waarmee wij met minder zink een dubbele bescherming bieden tegen roest. Naast de verzinklijnen is er ook over een verflijn.
Wij houden de kwaliteit van het staaloppervlak goed in de gaten. Geavanceerde en geautomatiseerde inspectiesystemen houden alles scherp in de gaten.
De cijfers
- Hoogte lussentoren: 30 meter
- Rollen staal: 1.6 miljoen ton verzinkt, waarvan 1/8 deel geverfde rollen
- Maximale snelheid van 180 meter per minuut
In de productielijnen van verpakkingsstaal wordt staal gebeitst, koudgewalst en gegloeid zodat het materiaal zachter en beter vervormbaar wordt. Zo is het geschikt om er bijvoorbeeld drankblikjes of spuitbussen van te maken. Het dunne plaatstaal krijgt hier ook een dun laagje tin om corrosie tegen te gaan. Daarnaast bekleden wij verpakkingsstaal met een dun laagje Protact® polymeer om het veilig te maken voor voedsel. Zo’n 95% van het verpakkingsstaal in Nederland wordt gerecycled tot nieuw staal. Blik is daardoor het meest circulaire en duurzame verpakkingsmateriaal.
De cijfers
- Productie van 0,8 miljoen ton per jaar, waarvan 95% vertind
- Dikte bandstaal: 0,14 – 0,5 mm
- 95% van de gebruikte blikjes wordt gerecycled tot nieuw staal
Op ons terrein vervoeren wij rollen staal van de ene productielocatie naar de andere. Uiteindelijk worden deze ingepakt om vanuit de vertrekhallen naar onze klanten te worden verzonden. Van al ons staal vertrekt:
- 1/3e per zeeschip
- 1/3e per binnenvaartschip
- 1/6e per trein
- 1/6e per vrachtwagen
De cijfers
- 100 kilometer aan spoor, 345 wissels en 90 kruisingen
- 350.000 rollen staal per jaar
Wij beschikken over een eigen energiebedrijf. Het voorziet ons van productiegassen, stoom en elektriciteit uit eigen centrales.
Productiegassen zijn bijproducten uit de Kooks- en Gasfabrieken, Hoogovens en Staalfabriek. Hiervan wordt tweederde door ons zelf (her)gebruikt. Het overige deel gaat naar de elektriciteitscentrale van Vattenfall die ons in ruil elektriciteit teruglevert.
De cijfers
- Wij produceren 15% van onze eigen elektriciteitsbehoefte
- Hoogovengasleiding is 2,5 km lang en heeft een doorsnede van 3,2 meter